
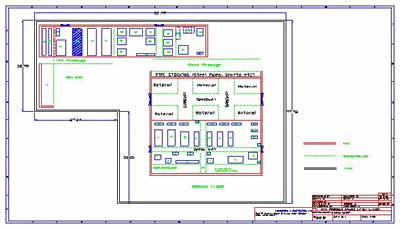
- PIPESIM SYSTEM REQUIREMENTS CODE
- PIPESIM SYSTEM REQUIREMENTS PLUS
- PIPESIM SYSTEM REQUIREMENTS SIMULATOR
The surface component includes the choke and surface pipe line. When the wellhead node is selected, the system is segmented into a surface component and a sub- surface component.
PIPESIM SYSTEM REQUIREMENTS SIMULATOR
Depending on the type of application, users may select from an extensive set of features to model a wide variety of fluid types.Ī number of Schlumberger and third-party applications are capable of generating PVT files that can be used by the PIPESIM simulator to interpolate fluid and transport properties. System Segmentation with Bottom-Hole Node. Steam can also be modeled as a single component system using the ASTM97 Steam Tables. The PIPESIM simulator offers the choice between industry-standard black-oil correlations or a range of equation-of-state compositional models. Fluid property modelingĪn accurate description of fluid behavior is critical to correctly model the production system. The PIPESIM simulator can also model internal natural convection using a proprietary methodology shared with OLGA.
PIPESIM SYSTEM REQUIREMENTS PLUS
Heat transfer models supported by the PIPESIM simulator include a flow regime dependent model for inside film coefficient, plus an analytical model for convection in buried and partially buried pipes-shown to closely match more complex finite-element methods. The PIPESIM simulator performs comprehensive energy balance calculations that account for a variety of heat transfer mechanisms, including the following: Heat transferĪccurate prediction of heat transfer is critical for calculating temperature-dependent fluid properties, prediction of solids formation and the overall thermal design of your system.

PIPESIM SYSTEM REQUIREMENTS CODE
The PIPESIM simulator includes code templates that can assist in compiling a user-generated 2- or 3-phase flow correlation via a plug-in DLL. High-resolution flow regime maps can also be produced for any point in the system. Additionally, the comparison operation can quickly sensitize to flow correlations and help selecting the most appropriate model. The PIPESIM simulator includes a calibration feature for flow correlation, which can automatically adjust the holdup factor, friction factor, and U-value multiplier to match measured pressures and temperatures. Additionally, the PIPESIM simulator predicts the risk of severe slugging in risers. The design of pipelines and processing facilities can be optimized by predicting hydrodynamic slugs, including size and frequency, as a function of length traversed. The PIPESIM simulator produces detailed flow regime maps at points of interest. These allow calculation of flow regimes, liquid holdup, slug characteristics, and pressure loss for all nodes along production paths of all deviations-vital information for designing and operating production gathering and distribution systems. The use of a number of different correlations to predict the hydraulic conditions of the dominant flow regimes in a pipeline system can result in numerical difficulties and/or discontinuous predictions.The PIPESIM simulator incorporates a wide variety of industry-standard multiphase flow correlations, as well as advanced 3-phase mechanistic models, including OLGAS, Kongsberg LedaFlow Point Model, and the TUFFP unified model. Individual equations tend not to apply with sufficient accuracy to the broad range of flow conditions usually encountered in practice. The limitations of empirical techniques stem from some or all of the following: Table 1 lists some of the more successful and widely-used correlations with recommended areas of application. Empirical correlations have been successful in terms of:Įnabling models for particular flow conditions to be formulated quickly.īeing amenable to tuning to yield results of reasonable accuracy over well-defined ranges of operating conditions.īeing relatively easy to employ as design tools. Other investigators such as Beggs and Brill,, and Dukler,, have correlated both variables ( f m, θ l) as functions of gas and liquid flow rates, pipe geometry, fluid PVT and transport properties, among other variables. The Hagedorn and Brown,, correlation for flow in vertical pipes is based on such an approach. Some authors of empirical correlations select an appropriate functional form for equation 1, and proceed to back calculate a holdup function that best fits experimental data for two-phase pressure drop. The second is a continuum approach in which more complex physically-based models are used to describe the flow phenomena.

The first is a global approach that relies on empiricism in developing simplified models that contain parameters which are evaluated from experimental data. Two distinct approaches are available to the petroleum engineer in accounting for the behavior of multiphase flow systems.
